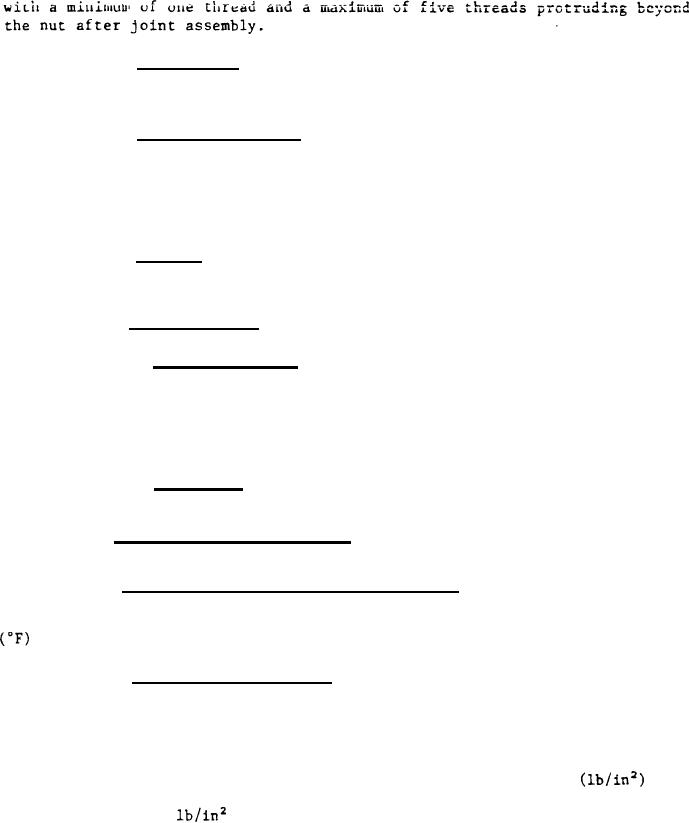
MIL-V-24642(SH)
3.4.11.3.1 Bonnet flange cap screws shall have a minimum length of one
diameter of fully formed threads engaged in the body of the valve. Lead and
vanishing threads shall not be counted as fully formed threads.
3.4.11.3.2 Where stud bolts are used, the nuts shall be fully engaged
3.4.11.4 Spot Lacing. Bearing surfaces of nuts and their respective
surfaces on the valve shall be finish machined or cast smooth and true
without nut interference.
3.4.11.5 Gland construction. The valve shall utilize a gland exhaust
connection. When this is connected to a vacuum of 10 inches of water in
accordance with 4.6.7, there shall be no visible leakage past the stem to
atmosphere under normal operating conditions. Visible leakage is defined as
an amount exceeding that which will form a fixed or stable meniscus or ring
of water. Packing shall not be allowed.
3.4.11.6 Gaskets. Spiral wound gaskets shall retain sufficient residual
load in service to maintain a leak-tight joint under system operating pressure
and temperature.
3.4.11.7 Internal trim.
3.4.11.7.1 Guiding surfaces. A difference in hardness of at least 100
points Brinell shall be maintained between the rubbing surfaces for main valve
guiding. This requirement shall not apply if both the guide, posts and bushings
are stellited or if the hardness of either exceeds 450 Brinell. Rubbing surfaces
for valve guiding shall have a finish of 32 or better in accordance with ANSI
B46.1.
3.4.11.7.2 Seat rings.
Seat rings shall be seal welded circumferen-
tially into the valve body.
3.4.12 Solenoid release mechanism. The unit shall utilize a 12 Vd.c.
electrical solenoid which when energized will cause the valve to trip closed.
3.4.12.1 Solenoid electrical characteristics. The electrical solenoid
shall be rated at 12 Vd.c. with a maximum current rating of 4.0 amperes (A).
The solenoid shall be designed for continuous duty at 185 degrees Fahrenheit
and classified as dripproof.
3.4.12.2 Manual reset mechanism. Reset of the valve from the trip to
the open position shall be accomplished in 25 seconds or less by means of a
threaded stem and handwheel device. Clockwise rotation of the handwheel to
a positive stop position shall allow manual engagement of the latch mechanism.
Counterclockwise rotation of the handwheel shall then allow the latch mechanism
to lift the valve to the fully open position. The 1,500 class valve shall open
against a pressure differential of 1,200 pounds per square inch
acting
on the top of the disc. The 600 class valve shall open against a pressure
differential of 600
acting on top of the disc.
1500 and 600 class valve
openings shall be accomplished by one person without mechanical aid.
8
For Parts Inquires call Parts Hangar, Inc (727) 493-0744
© Copyright 2015 Integrated Publishing, Inc.
A Service Disabled Veteran Owned Small Business